دسته: کارآموزی
بازدید: 2 بار
فرمت فایل: doc
حجم فایل: 3278 کیلوبایت
تعداد صفحات فایل: 71
گزارش کاراموزی بیمارستان امدادی واحد مالی در 71 صفحه ورد قابل ویرایش
قیمت فایل فقط 4,000 تومان
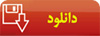
گزارش کاراموزی بیمارستان امدادی واحد مالی در 71 صفحه ورد قابل ویرایش
فهرست
مقدمه
الزامات چارت بیمارستان پایلوت
شرح وظایف هیات رئیسه
شرح وظایف کلی مدیر عامل
شرح وظایف واحد بودجه و امور مالی
شرح وظایف واحد فناوری مدیریت اطلاعات
شرح وظایف واحد مدیریت منابع انسانی
شرح وظایف واحد خدمات
شرح وظایف نگهداشت
شرح کامل نرم افزار بیمارستان
فرم های کار آموزی
مقدمه:
یکی از مشکلات اساسی بخش دولتی در بسیاری از کشورها این است که برونداد مورد انتظار از افراد یا واحدهای ارائه دهنده خدمات (نظیر بخشها، بیمارستان ها یا واحدهای مراقبت اولیه) در قبال اعتبارات اعطا شده به آنها تعریف نشده است. بخش دولتی بر مبنای حسابداری نقدی کار می کند؛ تنها چیزی که از نظر درستکاری و پاسخگویی اهمیت دارد این است که هزینه ها به نحو صحیحی صرف شده و به هدر نرفته باشند. اینکه تا چه حد بروندادی به ازای این سرمایه حاصل شده است؛ در درجه دوم اهمیت قرار می گیرد و معمولا هرگز محاسبه نمی شود. معنای این امر آن است که کارائی، اندازه گیری نمی شود و در نتیجه به سختی می توان دریافت که به چه میزان پیشرفت ایجاد شده است. این مسئله در مورد برابری نیز صدق می کند زیرا بخش دولتی سنتی، نمی تواند بخوبی تعیین کند که چه کسی از این برونداد بهره مند می شود.
در این میان یکی از مهمترین ابزارهای که می تواند در ایجاد تعهد در بین سطوح مختلف یک تشکیلات موثر باشد توافقنامه هایی است که بین این بخشها به ثبت می رسد و بوسیله آن علاوه بر واضح کردن حدود وظایف و انتظارات موجود بین طرفین، این حدود و وظایف جنبه قانونی و حقوقی به خود می گیرد. بحث پرداخت بر عملکرد عمدتا شامل تهیه، تنظیم و عقد توافقنامه هایی است که بالتبع بحث نظارت و ارزیابی نتایج کمی و کیفی اقدامات انجام شده در قالب پیمان و تعهدات طرفین را نیز در پی خواهد داشت.
«مدیریت عملکرد کارکنان» روشی است که اگر چه طور ظهور آن پدیده تازه ای نیست ولی در دو دهه اخیر بطور جدی و با یک نگاه کاملا نو مورد توجه قرار گرفته است. احتمالا دلایل این رویکرد درباره، برخی خصوصیات منحصر به فرد این روش است که آن را از دیگر روشها متمایز می کند. مدیریت عملکرد کارکنان را می توان در یک محیط با حداقل پیش زمینه های لازم به اجرا در آورد، در نتیجه در بیشتر سازمانها قابل پیاده کردن است. این روش مدیریت منابع انسانی نظام مند بوده و در صورت طراحی مناسب، نتایجی را در حداقل زمان ممکن ارائه می کند. عقد توافقنامه می تواند ابزاری برای اجرای سیاستها و ایجاد انگیزش ها جهت بهبود توزیع، بکار گیری و هزینه، اثر بخشی خدمات سلامت باشد.
شواهد کمی وجود دارد مبنی بر اینکه قرار دادهای خدماتی بخش دولتی خصوصی شرایطی را دارا باشند دهندگان انتفاعی و غیر انتفاعی را نسبت به عملکرد شان پاسخگو گرداند. از سوی دیگر پرداخت کنند گان عمومی، بودجه سازمانها دولتی را تامین می کنند تا ظرفیت های موجود حفظ نمایند (پرداخت حقوق ها و هزینه های جاری)؛ به جای تضمین اینکه مصرف کننده واقعاً خدماتی با کیفیت بالا دریافت نماید. نتیجه این است که سازمانها ی ارائه دهنده خدمات تمایل دارند که انرژی خود را به جای بهبود کارائی یا کیفیت خدمات به حفظ دارائی ها اختصاص دهند. از طرفی کمبود پاسخگوئی در سیستمهای بهداشتی، که بوسیله شاخصهای دسترسی، سطوح تولید، کیفیت، کارائی و سایر شاخص ها اندازه گیری می گرد، عملکرد را به همراه خواهد داشت.
مشکل بزرگی که در حال حاضر گربیان گیر بسیاری از سازمانها و تشکیلات دولتی، نیمه دولتی و حتی بخش خصوصی می باشد عبرتی است بنام «نارضایتی فراگیر»!!!................... به بیان دیگر در این سازمانها کلیه سطوح اعم از مدیران و کارکنان همگی از یکدیگر ناراضی هستند و هر یک مشکلات موجود را ناشی از سوء عملکرد گروههای دیگر می دانند. این موضوع می تواند طیف وسیعی از عواقب وحشتناک را در پی داشته باشد که از «کاهش کیفیت زندگی شغلی» تا افت بهره وری و سوخت سرمایه های گرانقدری، که می توانند به عنوان میراث ما برای نسل آینده سازندگی ایجاد کنند را شامل می شود.
اگر چه ممکن است در سبب شناسی این مشکلات، بیش از یک منفرد مطرح باشد، شاید بتوان اذعان نمود بیشتر این ناهنجاریها به «ابهام» و «عدم تفسیر صحیح» از عملکرد و توقعاتی که افراد از خود و سایر اجزا سازمان دارند بر می گردد. یقیناً یافتن مدیرانی که ناکامی های خود را ناشی از عدم توانمندی کارکنان خود می دانند مشکل نیست؛ و به همین نسبت کارمندان بی شماری وجود دارند که معتقدند نه تنها مشکلات سازمان، بلکه بسیاری از مشکلات جامعه ناشی از سوء مدیریت رهبران سازمانی می باشد. این منازعات و اختلاف نظرها ناشی از چه چیزی می تواند باشد، در صورتی که انتظارات و مسئولیتها در یک تشکیلات بدرستی شفاف سازی نشود راه برای سوء تفاهمات و حاشیه روی ها عناصر مختلف سازمانی هموار شده و هر یک از اجزاء، که در شکل مناسب خود باید به یک سمت واحد (ارتقا، موفقیت و بقاء سازمان) حرکت نمایند، شکل آشفته ای به خود گرفته و باعث بروز مسائلی همچون معضلات ذکر شده خواهند گردید. این همان چیزی است که باعث شده است اخیرا بحث «مدیریت مبتنی بر عملکرد» مجدداً مورد توجه محافل علم مدیریت قرار گیرد.
در مدیریت مبتنی بر عملکرد بخش اعظم توان مدیریت بر «اداره» صحیح «عملکرد» اجزاء سازمان متمرکز شده و سعی بر این است که به جای معیار قرار دادن بسیاری از ملاکهای منسوخ شده مدیریت سنتیف همچون تکیه بر ظواهر و سلیقه ها، به دستیابی به تعریف واحدی از موفقیت در سازمان روی آورده و برای فعالیتهایی که جهت رسیدن به این موفقیت لازم است «شاخص» یا «متری» تعیین نمود تا کار آیی هر یک از عناصر در پیشبرد سازمان به این سمت مشخص گردد. چرا که در غیاب این «متر» هر کس می تواند نتیجه کار خود را توجیه نماید.
همچنان که در بیشتر چارچوبهای ارائه شده برای مدیریت مبتنی بر عملکرد اشاره شده است حداقل شرط برای تضمین بقاء سازمان طرح یک تعریف واحد از موفقیت سازمان و سپس تعیین شاخصهای عینی جهت سنجش میزان حصول هر یک از بخشهای دستگاه به این قبله واحد می باشد.
در این میان یکی از مهمترین ابزارهایی که میتواند در ایجاد تعهد در بین سطوح مختلف یک تشکیلات موثر باشد توافقنامه هایی است که بین این بخشها به ثبت میرسد و بوسیله آن علاوه بر واضح کردن حدود وظایف و انتظارات موجود بین طرفین، این حدود و وظایف جنبه قانونی و حقوقی به خود می گیرد. بحث پرداخت مبتنی بر عملکرد عمدتاً شامل تهیه، تنظیم و عقد توافقنامهایی است که بالتبع بحث نظارت و ارزیابی نتایج کمی و کیفی اقدامات انجام شده در قالب پیمان و تعهدات طرفین را نیز در پی خواهد داشت.
توافقنامه های مبتنی بر عملکرد با ایجاد وضوح در انتظارات طرفین از عملکرد (فرد متعهد برای ارائه خدمات) و پرداختها (توسط سفارش دهنده خدمت) به عنوان یکی از مهمترین ابزارهای مدیریت عملکرد کارکنان شناخته شده اند. هدف توافقنامه معرفی روشی بهتر برای دستیابی به عملکرد مناسب و پاسخگویی است، روشی که اهداف ارائه خدمات را دو شادوش بودجه به پیش میبرد.
مدیریت عملکرد در معنی واقعی خود این هدف را دنبال میکند که مدیران را باز ابزاری تجهیز نماید تا در هر لحظه عینی از نحوه عملکرد کارکنان، و اصولاً سازمان خود، در اختیار داشته باشند و متعاقبا این امکان میسر گردد تا به این وسیله مداخله های مدیریتی بشکل مستدل و قابل توجیهی به مرحله اجرا برسند.
در بیشتر رویکرد های جاری بر مدیریت عملکرد میتوان رد پای تلاش برای تعیین اهداف و برنامه های سازمانی و نهایتاً دستیابی به یک معیار عینی برای کلیه فعالیتهای انجام شده در قالب فرآیندهای سازمان را یافت. بدین ترتیب میتوان اغلب تصمیمات و اقدامات مدیریتی و نیز امر مهم تخصیص منابع را بر پایه مستندات و شواهد به مرحله اجرا در آورد (شکل 1 . 1 ).
روشهای اجرای توافقنامه ها، در کنار ابزارهای مختلفی که به تعیین شاخصهای عملکرد می انجامد، از مهمترین دستاویز ایی هستند که در یک مدل مناسب مدیریت عملکرد مورد توجه قرار میگیرند. توافقنامه ها، پیمان نامه ها و قرار دادها شیوه هایی هستند که مدیران بوسیله آنها میتواند سطوح انتظارات خود را برای مجموعه هایی که برنامه های عملیاتی سازمان را به مرحله اجرا میگذارند روشن نموده، و در مقابل، سطوحی از انتظارات (مالی و ...) طرف مقابل، که در صدد تامین آن هستند را، شفاف نماید.
الزامات اجرای طرح :
از مهمترین سیاست های تبیین شده توسط دولت جمهوری اسلامی ایران ارائه خدمات با کیفیت هر چه مطلوبتر به آحاد جامعه (عدالت اجتماعی) پاسخگوئی همه افراد در مقابل مسئولیت ها و اختیارات آنها و از همه مهمتر جلب رضایت مردم می باشد. بنظر می رسد که دستیابی واقعی به این موارد مهم، جز با بازنگری و ایجاد برخی تغییرات اصلاحی در رویه ها و سیستم های موجود ممکن نباشد. از آنجایی که منابع انسانی توانمند، آگاه و با انگیزه اساسیترین سرمایه های یک نظام ارائه خدماتی (بخصوص خدمات بهداشتی - درمانی) محسوب می شود، محور قرار دادن ایجاد اصلاحات در این بخش از اولویت های مهم بشمار می آید. خط مشی کلی ارائه شده در برنامه پنج ساله سوم توسعه نیز موکد این نکته است و از این رو در طی آن همه سازمان ها و نهادهای وابسته ملزم شده اند تا ضمن در نظر داشتن ارتقاء کیفی خدمات جهت گیریهای استراتژیک خود را بی استفاده بهینه از منابع و توجه به نتایج قرار دهند.
بر اساس الزامات قانونی و علمی و تجربی بسیاری که وجود دارد عملکردی نمودن فعالیت ها به عنوان یک دستور العمل کشوری در دستور کار سازمانها و ادارات دولتی قرار گرفته است، این الزامات عبارتند از :
الف ) الزامات قانونی
قانون برنامه توسعه سوم،
فصل اول – ماده – 1 بند ب – ردیفهای 6 و 7 و .8
فصل اول – ماده .3
فصل بیست و پنجم – ماده – 192 بند ب (.قانون پرداخت کار مزدی)
فصل بیست و پنجم – ماده 93
ضوابط اجرایی تنظیم مقررات مالی دولت، ماده 88
مصوبات هیات محترم وزیران، بند 9
سیاستهای استراتژیک وزارت متبوع ،شماره 9 و . 16
فصل یازدهم ماده 68 – 67 لایحه خدمات مدیریت کشوری
ماده 145 قانون برنامه چهارم توسعه
ماده 228 قانون برنامه چهارم توسعه . بنده
ب ) پیشینه علمی و تجربی
بحث مدیریت و پرداخت مبتنی بر عملکرد در بسیاری از کشورها مسئله ای جدید نمی باشد و ضمن اجرا مسئله قانونی شدن و اجرای مقررات مربوط به آن نیز مورد توجه قرار گرفته است. به عنوان مثال :
در انگلیس از سال 1968 سیستم پرداخت بر مبنای عملکرد در مورد کارمندان کلینیک ها از جمله پرستاران و ماماها و سایر بخشهای عمومی و اجتماعی بکا گرفته می شود.
در نیوزلند از سال 1980 سیستم های عقد پیمان، جزئی اصلی از سیستم گسترده تر تخصیص منابع می باشد. در سال 1990 ، انجام پیش آزمائشی دو ساله ای را در مورد برخی خدمات ) .... Phc, Surgical که منجر به افزایش پاسخگویی ارائه دهندگان خدمت در کلیه نظام سلامت کشور شد.
در دانمارک از سال 1992 عقد پیمان بین سازمان و اجراء آن در جهت نیل به بهبود کارآیی و افزایش توان نظارتی و کنترل سیاستگذاری و بعنوان رویکردی متمرکز بر نتایج و مکمل سیستم بودجه بندی مورد استفاده قرار می گیرد.
در فنلاند از سال 1995 شبه قرار داد هائی بین وزارت خانه ها و فراهم آورندگان خدمت با هدف افزایش رضایت مشتریان و کارآیی و بهره وری سازمانی تنظیم می گردد.
در نروژ از سال 1990 بر سنجش عملکرد و ارتباط آن با انواع پرداخت ها تمرکز شده است و توسعه پیمان نامه های عملکردی توسط آئین نامه های جدید مالی تشویق می گردد.
در فرانسه از سال 1990 عقد پیمان در دو حیطه : 1 ) ایجاد یک چار چوب با توجه به نیاز ها و ملاحظات منطقهای سازمان جهت تدوین استراتژیهای قابل انعطاف و 2 ) بهبود عملکرد مورد استفاده قرار می گیرد.
در کانادا از همه نود توافقنامه های مشارکتی درون ادارات کانادائی جهت شناسائی درون داداها، بر روندها و نتایج مورد انتظار و ایجاد و ایجاد مکانیسمی برای اندازه گیری پیامد های به کار برده می شود.
در بلژیک از اوایل دهه نود بهره وری خدمات عمومی و شرایط ارائه این خدمات با تمرکز بر کاهش هزینه و افزایش کارآیی تاکید می گردد.
اسپانیا در مرحله توسعه مدیریت پیمان بعنوان جزئی از روند مدر نیز اسیون و اصلاح سیاستهای سیاسی و مدیریتی با هدف : افزایش کارائی، ارائه خدمات مطلوبتر به مشتریان، ایجاد شفافیت و درک بیشتر در اهدف، نقشها و مشئولیتهای مالی طرفین پیمان، کاهش هزینه ها می باشد.سوئد از سال 1981 به تغییر نظام پرداخت در جهت «باز پرداخت بر مبنای عملکرد» اقدام نموده است .
کنیا از سال 1992 ، پرداخت بر مبنای عملکرد را ابتدا در بیمارستان Kenyatta National Hospital بکار برده است.
مالزی از سال 1994 اقدام به پرداخت بر مبنای عملکرد ابتدا در Heart Ins National نموده و سپس آن را در سایر زمینه ها گسترش داده است.
هند در سال 1995 ، از مدیریت عملکرد و پرداخت بر مبنای عملکرد ابتدا در زمینه Reproductive Health استفاده نموده است.
آلبانی از سال 1995 ، در فعالیتهای Primary Care Services & Drugs از پرداخت بر مبنای عملکرد بهره می گیرد.
مدیریت مبتنی بر عملکرد فرآیندی است که به واسطه آن می توان در مورد آنچه سازمان باید به آن دست یابد و چگونگی رسیدن به آن، درکی واحد و زبان مشترک ایجاد نمود. و مدیریت عملکرد کارکنان (PPM)نآاااا
جزئی از مدیریت مبتنی بر عملکرد و راهکار جدبد سازمانی مدیریت عمومی می باشد که کارکنان و مدیران را فرآیند کنش متقابل هدف های اجرائی، معیارهای پاسخگوئی و کردار های تکامل یابنده برای بهبود مهارتها و عملکرد آینده، به تلاش فرا می خواند.
مدیریت عملکرد کارکنان بر این باور بنا شده است که کارکنان و مدیران صف بزرگترین منبع موسسه عمومی به حساب می آیند و از طریق راهکار های زیر در پی ارتقای عملکرد بخش عمومی می باشد:
درگیر کردن مستقیم تر کارکنان در استقرار هدفهای حرفه ای خود
پیوند دادن کارکنان به رضایت دیگر اعضای تیم و همچنین مشتریان
دادن سهم بیشتری از دستاوردهای سازمان به کارکنان
ارائه پاداش های مناسب به مجریان برتر (پرداخت پاداش اضافی) و خود داری از پرداخت اضافی به کارکنان در مقابل عملکرد ضعیف
یکی از گامهای نیل به اهداف (PPM) واگذاری از طریق پیمان کاری مبتنی بر عملکرد می باشد. که فرآیندی برای اولویت بندی و جهت دهی هدف پیمان کار با استفاده از توافقنامه به عنوان اساس ارزیابی و ادواری می باشد. در حال حاضر عقد توافقنامه در بسیاری از کشور ها به عنوان مقدمه یک فرآیند مدیریت عملکرد کارکنان تلقی می شود.
با هدف اجرای الزامات قانونی موجود مبنی بر عملکردی نمودن فعالیتها و با هدف شایسته سالاری، عدالت تخصیص منابع، افزایش انگیزه، دستیابی به عملکرد مناسب، ایجاد پاسخگویی بیشتر، ایجاد احساس عدالت در پرداخت ها، بالا بردن بهره وری پرسنل و جهت دار نمودن فعالیتهای کارکنان، تلاش در جهت عملکردی نمودن و تکیه بر نتیجه فعالیتها در دستور کار وزارت بهداشت، درمان و آموزش پزشکی قرار گرفته است.
لیکن با توجه به اهمیت موضوع و خطرهای بالقوه در اجرای این نظام بدلیل احتمال ایجاد تاثیرات معکوس (در صورت انجام هر گونه اقدام نسنجیده) این طرح در دو مرحله پایلوت گردیده است. مرحله اول در بیمارستان ضیائیان تهران و از طریق یک الگوی 6 مرحله ای به انجام رسید و سپس با توجه به دستاورد های حاصل از انجام این پایلوت و مطالعات گسترده ای که از منابع داخل و خارج کشور صورت گرفته بود یک الگوی ایرانیزه شده ارائه گردید که در حال حاضر در 40 بیمارستان کشور در حال پایلوت است.
از آنجائیکه بدلیل نبودن زمینه و ساختار های مناسب، اجرای تمام گام های مدیریت مبتنی بر عملکرد در قالب یک طرح کاری بسیار دشوار به نظر می رسید. لذا با توجه به پیشینه علمی و نتایج بدست آمده از مطالعات و اجرای پایلوت اول و پس از اعمال تغییرات اساسی در الگوی اولیه ) مدل 6 گامی (، با توجه به بررسیهای انجام شده و مطالعه الگوهای مختلف در کشور های توسعه یافته و در حال توسعه مدل زیر در وزارت بهداشت طراحی گردید و به اجرای آزمایشی درآمد. تمرکز اصلی الگوی جدید بر روی سیستم پرداخت عملکرد و مدیریت پیمان از طریق عقد توافقنامه های عملکرد ابزار اساسی ایجاد پاسخگوئی) می باشد.
لازم بذکر است هر چند الگوی اجرا شده در کشور ما حاصل بررسی های انجام شده در کشورهای مختلف از جمله NHS انگلستان، کانادا و ...... می باشد لیکن با توجه به شرایط ایران بومی شده است . در حقیقت این الگو با هیچ یک از الگوهای اجرا شده در دنیا به طور کامل و 100% مطابقت نمیکند.
اجرای نظام مدیریت مبتنی بر عملکرد در بیمارستانهای پایلوت کشور طی مراحل ذیل صورت میپذیرد:
اطلاع رسانی، آموزش و توجیه کلیه افراد درگیر (فرهنگ سازی)
از آنجا که مقاومت در برابر هر نوع تغییر و نوآوری در یک سیستم اجتناب ناپذیر می باشد، اجرای طرح مدیریت عملکرد نیز از این قاعده مستثنی نبوده است. از اینرو در اولین گام اجرائی از طریق ارائه آموزشهای لازم در زمینه ضرورت، فواید و اصول اجرای مدیریت پیمان و توافقنامه به کاستن مقاومت افراد (در بالاترین سطوح مدیریتی تا کارکنان اجرائی در بیمارستانها) با هدف فرهنگ سازی، توجیه و ایجاد انگیزه در آنان جهت پذیرش تحولات جدید پرداخته شد.
این آموزشها در قالب برگزاری سخنرانی، سمینار، کارگاه آموزشی، تشکیل کمیته های عملکردی، انتشار کتب، مقالات و پوستر ارائه گردید.
تبصره 8 : رئیس دانشگاه می تواند دستور منحل شدن هیات رئیسه بیمارستانهای آموزشی را صادر نماید.
تبصره 9 : حداقل دو معاونت از معاونت های درمان و آموزشی و پشتیبانی با دلایل مستند می توانند درخواست منحل شدن هیات رئیسه بیمارستانهای آموزشی را از رئیس دانشگاه بنماید.
تبصره 10 : رئیس خدمات درمانی مسئولیت خدمات درمانی سر پایی و درمانگاه را نیز عهده دار است.
تبصره 11 : کارشناس مسئول فن آوری اطلاعات بر بعد اطلاعاتی مدیریتی واحد مدارک پزشکی نظارت دارد.
شرایط لازم برای عضویت در هیات رئیسه بیمارستان :
شرایط لازم برای عضویت در هیات رئیسه بیمارستان داشتن حداقل مدرک کارشناسی برای کلیه اعضاء هیات رئیسه می باشد.
شرح وظایف هیات رئیسه :
1 ) تعیین خط مشی، اهداف، ماموریت بیمارستان و تایید برنامه استراتژیک بیمارستان
2 ) نظارت بر اجرای برنامه عملیاتی بیمارستان
3 ) تصویب برنامه های ارائه شده از سوی مدیر عامل بیمارستان
4 ) اتخاذ تصمیم و ارائه راه کار های علمی و عملی مناسب و به هنگام قبل و پس از وقوع بحران
5 ) بررسی و تصویب بودجه پیشنهادی مدیر عامل بیمارستان
6 ) تصویب تغییرات پیشنهادی در مورد تشکیلات تفضیلی بیمارستان بوسیله مدیر عامل بیمارستان
7 ) استقرار نظام پرداخت مبتنی بر مبنای عملکرد در بیمارستان
8 ) تصویب پیشنهادات مربوط به توسعه بیمارستان
9 ) پاسخگویی به مشکلات خارج از بیمارستان
10 ) جلب همکاریهای برون سازمانی و مردمی
11 ) نظارت بر روند ارزیابی فعالیتهای بیمارستان و تصویب شاخصهای عملکردی بیمارستان
شرایط عمومی در مورد پست مدیر عامل :
ماده 1 : مدیر عامل بیمارستان های پایلوت به پیشنهاد کمیته استانی و صدور ابلاغ از سوی ریاست دانشگاه منصوب می شود.
ماده 2 : مدیر عامل در بیمارستانهای غیر آموزشی (شهرستانها) به پیشنهاد کمیته استانی و صدور ابلاغ از سوی معاونت درمان دانشگاه منصوب می شود....
ماده 3 : مدیر عامل بیمارستان در مقابل رئیس دانشگاه پاسخگو می باشد. اما رابطه مدیر عامل با هیئت رئیسه رابطه رئیس و مرئوس نیست و هیئت رئیسه تصمیم ساز و مدیر عامل تصمیم گیر است.
شرایط احراز پست مدیر عامل :
داشتن مدرک تحصیلی کارشناسی ارشد مدیریت خدمات بهداشتی درمانی با 2 . 3 سال سابقه کار اجرایی
داشتن مدرک تحصیلی Ph.D مدیریت خدمات بهداشتی درمانی با 2 سال سابقه کار اجرایی
پزشک عمومی یا متخصص با گذراندن حداقل 2 سال دوره مدیریتی و سابقه کار اجرایی و یا حداقل 5 سال سابقه کار اجرایی در رده های مدیریتی
تبصره 1 : پیش بینی پرداخت متعارف و مناسب به مدیر عامل، با نظر و تصویب کمیته استانی، به نحوی که انگیزه کافی برای قبول مسئولیت با حذف دقت کافی به وجود آید.
تبصره 2 : مدیر عامل بیمارستان بایستی به صورت تمام وقت در خدمت بیمارستان باشد و در طول دوران اجرای طرح پایلوت (سال 83 ) مجاز به انجام کار انتفاعی در خارج از بیمارستان حتی در سایر بیمارستانهای دانشگاه نمی باشد.
شرح وظایف کلی مدیر عامل :
مدیر عامل بیمارستان مسئولیت چرخش کار بیمارستان مطابق اختیاراتی که دارد بر عهده دارد.
باید موجبات پیروی سازمان را از قوانین و مقررات ذیربط فراهم آورد.
باید در مورد بازنگری و اجبات فوری، پاسخگویی به گزارشها و توجیه های مربوط به برنامه ریزی مراجع بازرسی، مطابق ضوابط هیئت رئیسه اقدام کند.
باید با مجموعه خدمات توسعه مدیریت، هیئت پزشکی و اداری بیمارستان کار کند و با ترسیم خطوط مختلف و اداره بیمارستان موجبات مدیریت مطلوبی را فراهم آورد.
مدیر عامل بیمارستان باید ضمن کار با مدیران مسئول، اعضای بالینی، امور پزشکی، و اداری بیمارستان موجبات و امکانات نظارتهای لازم را بر حمایت از جان انسانها، و منابع مالی و اطلاعات و داده ها فراهم آورد.
بستر سازی استراتژیهای پنجگانه پروژه اصلاح ساختار اقتصادی مدیریت بیمارستان
شرح وظایف اختصاصی مدیر عامل :
مسئولیت کامل اداری و مالی بیمارستان
انتخاب مسئولین مجرب و صالح در بخشهای مختلف بیمارستان
مسئولیت منابع مالی و بودجه بیمارستان
مسئولیت تجهیزات پزشکی و تاسیسات بیمارستان
مسئولیت هدایت بیمارستان در اجرای برنامه های مصوب دانشگاه و هیئت رئیسه
مسئولیت نظارت بر کار کلیه بخشهای اداری، مالی، بالینی و پیرا پزشکی
مسئولیت نظارت بر مراقبت صحیح از بیمار
شرکت در جلسات هیئت رئیسه
شرایط احراز پست رئیس خدمات مدیریت :
ترجیحاً فوق لیسانس و لیسانس مدیریت خدمات بهداشتی درمانی
در صورت نبود فارغ التحصیلان مزبور فوق لیسانس و لیسانس مدیریت دولتی با حداقل سوابق اجرایی 2 سال (فوق لیسانس) 4 سال (لیسانس)
شرح وظایف پست رئیس خدمات مدیریت :
مسئولیت نظارت بر قسمت فناوری اطلاعات
مسئولیت نظارت بر قسمت منابع انسانی
مسئولیت نظارت بر قسمت نگهداشت
مسئولیت نظارت بر بودجه و امور مالی
مسئولیت نظارت بر خدمات و بهداشت
پاسخگویی و ارائه گزارشهای مربوط به واحد های ذیربط خود به مدیر عامل
مسئولیت هدایت بیمارستان در اجرای برنامه هایی که از طرف مدیر عامل به وی تفویض گردیده است.
شرکت در جلسات هیئت رئیسه
شرایط احراز کارشناس مسئول بودجه عملیاتی و امور مالی :
لیسانس یا فوق لیسانس در رشته های اقتصاد، امور مالی، حسابداری، مدیریتی (ترجیحاً مدیریت دولتی، مدیریت خدمات بهداشتی و درمانی)
فوق لیسانس رشته اقتصاد بهداشت
شرح وظایف واحد بودجه و امور مالی :
پیاده نمودن سیستم بودجه ریزی عملیاتی در بیمارستان
انجام امور مالی بیمارستان
ارائه بهترین ابزارهای ممکن بر اساس نتایج (به جای صرف داده ها و ستاده ها) در جهت بر آوردن احتیاجات ضروری مردم
ارائه اطلاعات قابل سنجش برای هیئت رئیسه که بتوان به استناد آنها میزان پیشرفت و موفقیت کارها را در مقابل تخصیص های بودجه کنترل نمود.
ارائه مبنای صحیح برای اتخاذ تصمیم در خصوص تخصیص منابع بیمارستان
تمرکز فرآیند تصمیم گیری روی مهمترین مسائل و چالشهایی که بیمارستان با آن مواجه است.
بودجه ریزی عملیاتی :
1 ) طبقه بندی عملیات
2 ) انتخاب واحد اندازه گیری
3 ) بر آورد هزینه یک واحد کار
4 ) پیش بینی حجم عملیات
5 ) محاسبه هزینه عملیات
شرح وظایف کارشناس مسئول بودجه ریزی عملیاتی :
پیشنهاد سیاستها و خط مشی ها در خصوص بودجه بیمارستان
پیشنهاد در خصوص اصلاح ساز و کارهای مالی بیمارستان
تهیه و تدوین گزارش و تنگناهای بودجه بیمارستان
تهیه و تدوین بودجه پیشنهادی و سالیانه بیمارستان
تهیه گزارش نتایج عملکرد بودجه ای بیمارستان و تعیین انحرافات بودجه ای (دوره ای موردی)
تهیه و تدوین گزارش تحلیلی از وضعیت شاخصهای اقتصادی بیمارستان
تهیه صورتهای مالی بر اساس حسابداری نقدی تا استقرار حسابداری تعهدی
کنترل هزینه ها و درآمدها و گزارشات مستمر مدیریتی
تهیه و تدوین نقطه سر بسر بخشها و تعیین کسری با مازاد هر مرکز هزینه
تهیه و تدوین نقطه سربسر بیمارستان
تفکیک هزینه های ثابت و متغیر بیمارستان
تهیه گزارشات مدیریتی جهت باز یافت منابع راکد بیمارستان
تهیه گزارشات هزینه های متورم جهت مدیریت
انجام سایر امور مربوطه طبق دستور مقام ما فوق
شرایط احراز کارشناس مسئول فناوری اطلاعات :
کارشناس یا کارشناسان ارشد کامپیوتر (نرم افزار)
فوق لیسانس رشته مدارک پزشکی
شرح وظایف واحد فناوری اطلاعات :
پیاده سازی سیستم HMIS در بیمارستان
مطالعه و بررسی، ارائه الگوهای مناسب و تلاش در جهت استقرار نظام های اطلاعاتی بیمارستانی و فناوری اطلاعاتی نوین در بیمارستان
تهیه استاندارد های سخت افزاری و نرم افزاری برای بیمارستان
19 ) انبار گردانی و شروع دوره جدید
20 ) تهیه لیست مغایرت موجودی کالا و کالاهای شمارش شده در انبار گردانی
21 ) امکان ارائه گزارش کالاهائی که به حد سفارش رسیده اند و یا گزارش از کالاهائی که دارای حداقل موجودی هستند.
22 ) امکان تهیه اتوماتیک درخواست خرید برای کالاهائی که به نقطه سفارش رسیده اند.
23 ) امکان گزارش از گردش کار کلیه کالاها در یک محدوده زمانی
24 ) امکان گزارش بر روی کالاهائی که گردش نداشته اند
14 ) سیستم مدیریت بیمارستان :
مدیریت بیمارستان از طریق کامپیوتر مستقر در واحد مدیریت به مجموعه اطلاعات ذیل دسترسی دارد اینگونه اطلاعات مدیریت را در کنترل لحظه ای عملیات بیمارستان، ارزیابی وضعیت موجود و انجام تصمیم گیری مقتضی کمک مینماید :
1 ) فهرست تختهای خالی در هر لحظه در بیمارستان
2 ) گزارش تعداد بیماران بستری شده، تسویه شده به تفکیک قرار داد در یک محدوده تاریخی
3 ) گزارش از تعداد اعمال انجام شده به صورت پارامتر یک در یک محدوده تاریخی
4 ) گزارش از تعداد مراجعین به صورت بستری و سرپایی به آموزشگاه همراه گزارش درآمد آن؛
5 ) گزارش از تعداد مراجعین به صورت بستری و سرپایی به رادیولوژی همراه گزارش در آمده آن؛
6 ) گزارش از تعداد مراجعین به صورت بستری و سرپایی به پاتولوژی همراه گزارش درآمد آن،
7 ) گزارش از نسخه های صادره داروخانه به همراه گزارش درآمد آن؛
8 ) گزارش هزینه یک بخش؛
9 ) گزارشات مختلف از نحوه عملکرد قسمت های مختلف به صورت پارامتر یک؛
10 ) امکان تعریف قرار داد برای بیماران بستری و سرپایی و تنظیم اتوماتیک صورت حساب بیماران؛
11 ) امکان تعریف اشتغال پزشک جهت جراحی یا بستری کردن بیمار و یا فعالیت های دیگر در بیمارستان،
12 ) کنترل درخواست کالاهای صادر شده و امکان تایید آنها؛
15 ) سیستم دبیر خانه و نامه نگاری:
سیستم دبیر خانه و نامه نگاری از امکانات زیر بهره می برد.
1 ) ثبت و نگهداری اطلاعات مربوط به نامه های وارده و صادره،
2 ) تعریف عنوان نامه ها جهت گزارش گیری و تعریف واحدهای بیمارستان؛
3 ) دفتر تلفن؛
4 ) دفتر یاداشت ها و پیامهای ضروری و هشدار دهنده در موعد مقرر؛
5 ) گزارشات متنوع از نامه ها و فرم ها به صورت های مختلف؛
6 ) امکان تایپ چاپ نامه ها و فرم ها به صورت های مختلف؛
7 ) امکان پیگیری نامه های وارد شده و جواب داده نشده و نیز آنکه نامه در چه قسمتی قرار دارد.
16 ) سیستم حسابداری مالی و حسابداری قرار دادی:
وظیفه این سیستم، تنظیم اسناد و ارائه دفاتر قانونی، دفتر کل و روزنامه و همچنین ارائه گزارشات مربوط به تراز های آزمایشی و عملکرد حساب ها می باشد. جهت دقت و سرعت بیشتر در امر تهیه اسناد مالی، سندها اتوماتیک از قسمتهای صندوق حسابداری، پزشکان، انبار و حقوق و دستمزد تهیه می گردد.
بطور کلی وظایف این سیستم به شرح زیر می باشد.
1 ) امکان ثبت سند موقت و ثبت معکوس سند بطور اتوماتیک؛
2 ) امکان تعریف کدینگ دفاتر کل، معین و تفضیلی به همراه پارامترهای حساب فوق؛
3 ) امکان گزارش گیری بر روی دفاتر معین در قسمت سپرده ها و کنترل و پاس شدن آنها؛
4 ) امکان ارسال پرونده قرار دادی به طرف قرار داد؛
5 ) امکان گزارش بر روی پرونده های قراردادی ارسالی و پرونده های قرار دادی دریافتی؛
6 ) امکان گزارش گیری و تهیه دفاتر کل، معین، روزنامه، عملکرد حساب خاص، تراز آزمایشی و حساب سود و زیان؛
7 ) امکان ارائه لیست مغایرت بانک و صدور چک و کنترل حساب های مربوط به بانک بطور جداگانه؛
8 ) امکان تهیه سند کلی دفاتر برای ارائه به دارائی؛
9 ) امکان کنترل روی پرونده های بیماران قرار دادی و تهیه گزارش از پرونده های ارسالی به بیمه؛
10 ) امکان ثبت پرونده های برگشت شده از شرکتهای بیمه و ثبت کسورات اعمال شده توسط آنان؛
17 ) سیستم حسابداری پزشکان:
وظیفه این سیستم، تفکیک حق الزحمه مربوط به پزشکان از بابت بیماران بستری، بیماران سرپایی و بیماران درمانگاهی می باشد. ورودی های این سیستم از قسمتهای ترخیص و صندوق می باشد و Data Entry اطلاعاتی زیاد ندارد.
سیستم حسابداری پزشکان دارای امکانات زیر می باشد.
1 ) کنترل اطلاعات پزشکان که از صندوق ترخیص دریافت شده و تائید آنها،
2 ) کنترل اطلاعات خدمات درمانگاهی پزشکان که از صندوق درمانگاه دریافت شده و امکان تائید اطلاعات،
3 ) امکان ارائه فیش درآمدی پزشکان به صورت کلی و آنالیز حساب با توجه به قرار داد پزشک؛
4 ) امکان ارسال اطلاعات ریالی پزشک به حساب مربوطه از طریق ارتباط مستقیم با سیستم بانک؛
5 ) امکان اعلام پرونده های قرار دادی پزشک برای بیمارانی که مرخص شده اند ولی تسویه شده اند؛
6 ) امکان درج کسورات مختلف پزشکان و اعمال در محاسبات آنها؛
18 ) سیستم صندوق درمانگاه:
وظیفه این سیستم، ارائه و صدور کلیه قبض های مربوط به درمانگاه، اورژانس و قسمت پارکینگ ها در مورد بیماران سرپایی می باشد. این قسمت با پارکینگ ها، مرتبط بوده و قبض های ثبت شده آنها بطور اتوماتیک، جهت عدم تشکیل صف و سرعت در امر صدور قبض بیمار می باشد.
امکانات سیستم به شرح زیر است.
1 ) ثبت کلیه فعالیتهای پارکینگ ها، درمانگاه و اورژانس به تفکیک؛
2 ) امکان تعریف کلیه فعالیتهای درمانگاه؛ اورژانس و تعریف کلیه پارکینگ ها با توجه به نوع بیمارستان؛
3 ) امکان تعریف قرار دادهای مختلف و نسبت دادن هر قرار داد به فعالیت مربوطه؛
4 ) امکان استفاده از چندین صندوقدار بطور همزمان و کنترل کلی اطلاعات آنها؛
5 ) امکان بستن حساب صندوق به تفکیک هر صندوقدار؛
6 ) امکان تعریف انواع صندوقهای و صندوقدار و سطوح دسترسی آنها به سیستم؛
19 ) سیستم پرسنلی و حقوق و دستمزد:
این سیستم کلیه عملیات و اطلاعات مربوط به پرسنل از جمله پرونده پرسنلی، احکام پرسنلی، مرخصی ها، وامها، حقوق و ...
دستمزد مکاتبات مربوط به پرسنل، تشویق و تنبیه را تحت کنترل دارد. برخی از امکانات این سیستم به شرح زیر می باشد.
1 ) تعاریف مربوط به کد های متغیر (ملیت، مذهب، نظام وظیفه، رشته تحصیلی، شهر، تاهل، مسکن، جنسیت، زبان خارجی، بانک، نوع مکاتبات)
کد های ثابت (مرخصی ها، ماموریت وام ها)
کد های حقوقی (مزایا، کسورات، نوع استخدام، نوع حکم)
کد های سازمانی (مرکز هزینه، قسمت، رشته، رسته)
کد های متفرقه (شیفت، سرویس) تعریف جدول مالیات، تعریف جدول بیمه، تعریف مشاغل سازمانی تعریف شرح پایه حکم، تعریف مکاتبات روتین، تعریف متغیرهای پایه،
2 ) ثبت اطلاعات مربوط به پرسنل و سوابق و تجربیات کاری بطور کامل،
3 ) ثبت اطلاعات مربوط به احکام پرسنلی و صدور احکام کلی به صورت پارامتر یک برای پرسنل،
4 ) ثبت اطلاعات مرخصی ها، ماموریت ها، تشویقات، تنبیهات، انفصال از خدمت و مکاتبات پرسنل،
5 ) ثبت اطلاعات حقوقی پرسنل و پردازش اطلاعات و انتقال اطلاعات از Io (سیستم حضور و غیاب)
6 ) محاسبات مربوط به عیدی و پاداش پرسنل؛
7 ) گزارشات مربوط به اطلاعات پرسنلی، احکام پرسنلی و پرونده پرسنلی بطور کامل با ذکر جزئیات،
8 ) گزارشات مربوط به اطلاعات حقوقی از جمله فیش حقوقی، لیست جامع مالی، دیسکت بانک و گزارش بانک، لیست بیمه و گزارش بیمه و گزارش وام پرداختی،
9 ) گزارش مربوط به مزایا و کسورات به شکل انتخابی و گزارش هزینه ها در مرکز هزینه،
10 ) گزارش کارت حقوقی کلیه پرسنل به صورت کلی و تک،
11 ) گزارش جامع حقوق و دستمزد به صورت مایه التفاوت و به صورت مقایسه ای،
12 ) گزارش افراد وارده شده به سیستم پرسنلی و حقوق و دستمزد،
13 ) اطلاعات مربوط به تقویم سیستم، بستن ماه و سال، گزارش روی ماهها و سالهای قبل؛
14 ) امکانات مربوط به دفتر تلفن، دفتر یاداشت، تنظیمات سیستم، ماشین حساب، تعریف کاربر،
20 ) برنامه اموال:
در این برنامه می توان دارائی های ثابت را تحت کنترل درآورد.
1 ) محاسبه استهلاک براساس تاریخ خرید،
2 ) ثبت تعمیر و یا ارسال به تعمیر گاه برای اجناس،
3 ) امکان ارتباط بین کد های اموال و کد های اجناس در انبار بیمارستان،
21 ) اورژانس:
1 ) پذیرش بیمار در قسمت اورژانس بیمارستان،
2 ) ثبت کلیه خدمات انجام شده روی بیمار در قسمت اورژانس،
3 ) چاپ گزارش از کلیه خدمات و لوازم مصرف شده روی بیمار،
4 ) تهیه گزارش از خدمات انجام شده برای بیماران،
22 ) پذیرش درمانگاه:
توسط این نرم افزار کارهای زیر را می توان انجام داد.
1 ) پذیرش بیماران مراجعه کننده به درمانگاه،
2 ) ثبت نسخه، رادیو گرافی و آزمایش برای بیماران درمانگاه،
3 ) صدور شماره قبض صندوق برای اعمال انجام شده روی بیماران،
4 ) تهیه گزارش از تعداد بیماران مراجعه کننده به درمانگاه،
23 ) کتابخانه :
توسط این نرم افزار کلیه امور مربوط به کتابداری را می توان در کتابخانه انجام داد و به صورت مکانیزه تحت کنترل درآورد.
1 ) امکان تهیه لیست کتابهای موجود در کتابخانه،
2 ) ثبت کتابهای که از کتابخانه توسط افراد بیرون برده می شود،
3 ) امکان اضافه نمودن کتابهای جدید به لیست کتابها،
4 ) امکان دسترسی آسان به مکان و قفسه ای که کتاب در آنجا قرار دارد.
24 ) مدیریت پرستاری:
در می توان امکانات زیر را به صورت ساده دارا شد.
1 ) گزارش از بیماران بستری در بیمارستان به صورت دقیق،
2 ) داشتن اطلاعات درست و دقیق از بخشها و تعداد بیماران هر بخش،
3 ) گزارش از تختهای خالی هر بخش،
4 ) تهیه گزارش از تعداد بیماران زن یا مرد،
در پایان لازم به ذکر است این طرح نیز مانند هر طرح مدیریتی دیگر در مرحله عمل با موانع و مشکلاتی روبرو می باشد که دستیابی به نتایج کامل را در بیمارستان ها با مشکل مواجه نموده است. از جمله این موانع می توان موارد ذیل را نام برد:
v کمبود اعتبارات مالی،
v عدم پرداخت به موقع تعهدات سازمانهای بیمه گر به بیمارستانها،
v عدم تعیین سرانه و تعرفه های واقعی خدمات بهداشتی درمانی،
v مشکلاتی ناشی از نبود نظام مناسب ثبت اطلاعات عملکرد و HIS در بیمارستان،
ماهیت حسابداری :
حسابداری که اغلب تجارات خوانده می شود روشهایی است قراردادی که توسط کارشناسان و استادان حسابداری و یا انجمنهای حرفه ای حسابداری تدوین گردیده، و به تدریج مورد قبول همگان قرار گرفته است؛ مقابل تغییر و تصحیح می باشد. در حسابداری، ما با بنیانگذاری یک مجموعه ظوابط و قراردادها می خواهیم اطلاعات لازم را برای حل مسائل مالی یک مؤسسه بدست آوریم.
اطلاعات حسابداری :
اطلاعات حسابداری یک سری اطلاعات مالی مربوط به مبادلات یک واحد تجاری است، که برحسب واحد پول بیان می گردد. رأی ثبت روز به روز این اطلاعات می توان از سیستم دستی یا مکانیکی و یا الکتریکی استفاده نمود.
فعالیت مالی :
منظور از فعالیت های مالی، آنگونه فعالیتهائست که به طریق موجب تغییراتی در دارائی، بدهی و یا سرمایه یک شخص، یا مؤسسه گردد. فعالیتهای مالی هر مؤسسه که در واقع مبادلات تجاری می باشد، اساس و مبنای عملیات حسابداری آن محسوب می شوند.
تعریف حسابداری :
«حسابداری عبارتست از فن تفسیر اندازه گیری و توصیف فعالیتهای اقتصادی».
(1987 – water B.Meigsobcrt.f.meigs)
ثبت فعالیتهای مالی :
در این مرحله کلیه داد و ستدها و فعالیت های مالی به ترتیب تاریخ وقوع در دفتری به نام دفتر روزنامه ثبت می شود در هر کشور فعالیتهای مالی بر حسب واحد پول همان کشور در دفات ثبت می گردد.